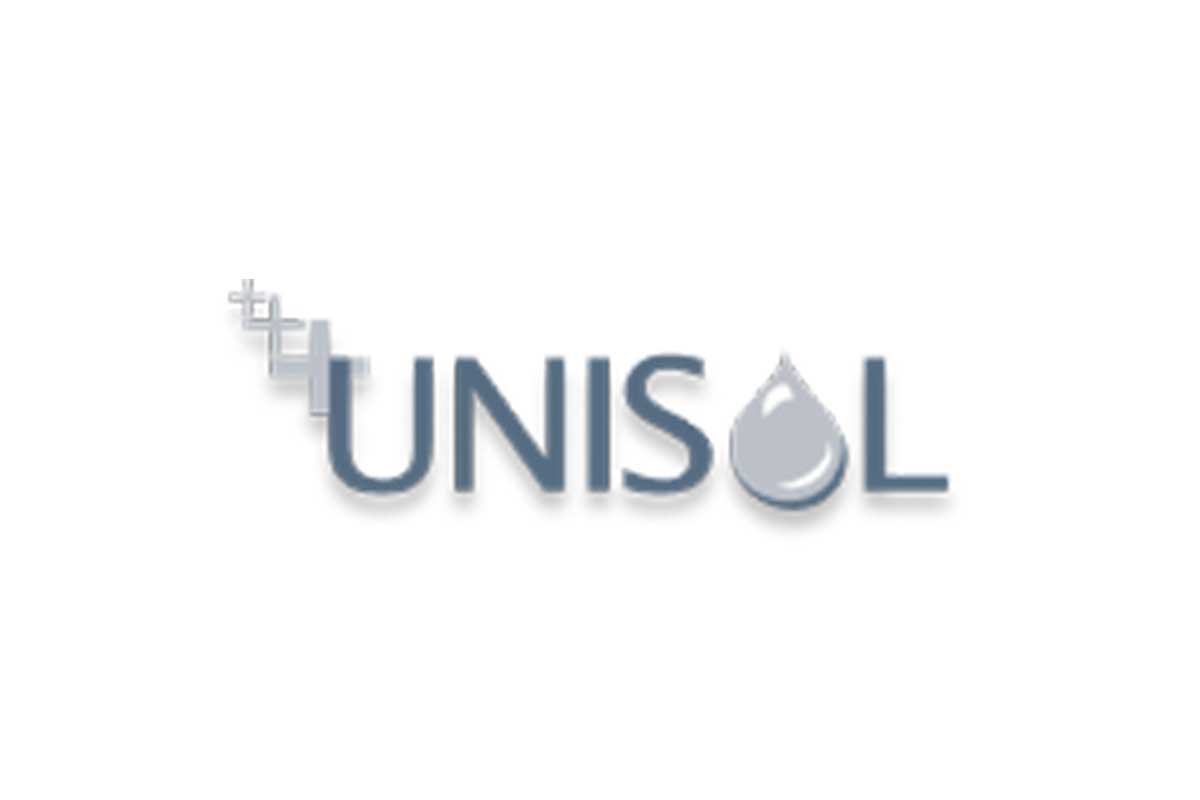
The dosage rate of the different products vary between 0.05 per cent (0.5Kg/t) and 0.15 per cent
(1.5Kg/t) of mill feed and the user can expect early age strength (one-day) to improve by up to 35 per cent and late age (28-day) to increase by up to 15 per cent. Mill throughput will generally be raised by 5-7 per cent. The use of STAREX has no negative impact on the durability of the final concrete.
The result of these physical benefits is that the user is able to increase cement extender content and reduce clinker content of the final cement with no impact on cement strength. The resulting financial benefit will pay for the additive and realise a financial benefit for the user. The alternative is that the user is able to use the improved cement
performance as a marketing benefit where the cement user could reduce the cement content of the concrete.
STAREX is typically supplied in powder form, which is ideal for conditions where the infrastructure to transport and handle bulk liquids does not exist. The product is supplied in 25kg polypropylene bags, which means that the product can be manually handled
if necessary. The dispensing of the powdered STAREX is done using manufacturer supplied dispensers which are accurate, simple to operate and maintain.
STAREX is a blend of highly ionized salts combined with dispersants and finely divided silica and zeolites. The mode of action of the product is that it accelerates C3S hydration with no impact on setting time; this translates into improved early and late age strength. The ionization of the salt helps to reduce agglomeration of cement particles in the mill system which results in more energy being available
for grinding which results in improved mill throughput or better particle size distribution.
A 2000tpd PPC operation The plant being discussed produces 2000tpd of PPC thorough a 90tph
cement grinding mill. The plant is located very close to a thermal power plant and has access to abundant fly ash. The landed cost of fly ash for the plant is quite low as the only price to pay is for the handling and transport of the ash.
Thermal power plants in India are not allowed to sell their ash and are supposed to let cement producers utilise it for free.
The content of fly ash is limited in PPC largely by its impact on the early age strength of the resulting
concrete. STAREX thus offers a very complimentary property with its positive impact on cement strength.
After multiple tests conducted at lab scale and plant scale, the benefits of dosing STAREX in the cement mill were clearly established. The plant now feeds STAREX into the cement mill
continuously along with clinker, fly ash and gypsum.
The impact of the additive on cement quality, fly ash content, and mill output is summarised in Table 1. The Table shows that STAREX has increased fly ash content by five per cent and improved cement performance at all stages of strength development. The mill output has also increased by around five
per cent. These physical benefits in turn have converted into commercial benefits – reduced cost of production, improved market response, and higher cement realisation.
Reduction in cost of production
The addition of STAREX allows the plant to add five per cent more fly ash while reducing the clinker content by the exact amount. This, combined with power saving due
to higher mill output, not only completely offsets the cost of STAREX but also offers additional cost savings.
Improved market response
Even after an increase in fly ash content and reduction in clinker content, the plant is
successfully able to deliver to an improved cement quality. The strength at
all ages is higher and is
gradually improving the brand image of the cement produced by this plant. With the supply glut expected over the next couple of years in the Indian cement industry, the improved brand image should keep the health of this cement plant’s business in good condition.
Higher cement realisation
STAREX has helped the plant successfully increase the cement mill output by around five percent. This in turn has a direct impact on the company’s realisation and income.
Reduced carbon footprint
Apart from the above mentioned benefits that directly impact the profits of the company, STAREX also delivers on a key environmental parameter, which is expected
to gain increasing significance in the times to come – reduced carbon footprint per ton of cement production. Every tonne of clinker produces 440kg of CO2. A reduction in clinker content by five per cent points in PPC translates into 22kg of CO2 saved per tonne of cement.
This turns into 13,200t of reduced CO2 emission over a year for the plant (based on 2000tpd production and 300 days of plant operation).
Dosing mechanism
The plant has deployed a gravimetric dispenser with
belt conveyor as recommended by Unisol Inc. for accurately dosing STAREX into the cement mill inlet. The dispenser is installed so that STAREX drops on the clinker weigh- feeder belt and goes into the mill inlet along with clinker.
The dispenser is equipped with a control panel and has been integrated with the DCS panel in the central control room of the plant. Thus the STAREX dosage rate and feed can be centrally controlled.
A picture of the dispenser and its local
control panel is provided in Figure 2.
The STAREX team
STAREX takes pride in the delivery of value to customers and potential customers. The company has a dedicated team of individuals who will introduce the product range
to cement producers globally and ensure that optimum value is added to customers’ businesses. The company has a track record of success and the product range is proved and trusted by cement manufacturers worldwide.
STAREX has offices and representatives in South Africa, Central Africa and India.
STAREX – South Africa
STAREX is headquartered in Johannesburg. The operations in South Africa include the manufacturing plant and a centralised R&D facility. STAREX South Africa is also involved in
processing of cement extenders such as fly ash, slag and silica fumes.
STAREX’s key markets are in the south and east.
STAREX – Central Africa
The company office in Central Africa is based in Nairobi, Kenya.
This office provides technical and operational support services to customers in the entire Central African region. The cement industry in this region is well developed and on a steep growth curve but faces substantial challenges relating to infrastructure availability. STAREX is used here by numerous customers, because of its ease of application and proven performance benefits.
STAREX – India (Unisol Inc)
STAREX in India and the Sub- continent is represented by Unisol Inc. The firm is headquartered in Gurgaon, a suburb of New Delhi,
and has offices and warehouses in multiple locations across India. Unisol Inc also has a local R&D facility to conduct basic cement performance tests. The key markets for Unisol Inc in the region include India, Nepal and Bangladesh.
Comments are closed.